LASER BEAM WELDING
A good fusion
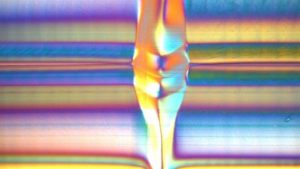
Laser beam welding has become increasingly established as an industrial joining technology in recent years. The advantages of laser technology speak for themselves: Through precise and flexible joining processes, we create mechanically resilient and – in the case of metallic materials – high-temperature-resistant and electrically conductive material-to-material joints. This holds great potential for the technological challenges of the future, for example in the field of electromobility.
Equipped with a wide range of laser beam sources, the appropriate guiding and positioning machines, and the necessary materials engineering and design know-how, we are ready for almost any welding task in both the metal and non-metal sectors:
– Conventional and remote laser beam welding in the micro and macro range
– Processing of different materials (same and dissimilar)
– Welding of difficult to weld materials
– Fine welding of filigree components
– Glass welding
Intelligent process sensors and analysis make it possible to detect and avoid errors during laser beam welding.
However, the state of the art is not enough for us: In numerous research collaborations we are working on extending existing limits in laser beam welding, for example in terms of robustness, processing speed and range of materials.
LASER SOLDERING
In the right solder
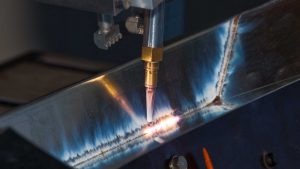
The demands on industrial joining technology are constantly increasing. A stable material joint is often not enough. The advantages of laser technology can be optimally utilized, especially in automotive engineering as well as in semiconductor, electronics or optoelectronics production. Post-processing-free as well as visually appealing seam connections in the visible range and precise joints on a microscale are the result of our projects for:
– Laser brazing of sheet metal and mechatronic components
– Laser beam soft soldering of electronic components
From track soldering in modern car body construction to brazing of power electronics, almost anything is possible thanks to intelligent process design and control. The virtually distortion-free joining of dissimilar materials using laser technology has already opened up many new fields of application. In order to further exploit the optimization potential with regard to process speed and quality in the future, we work with the most modern process monitoring methods and are continuously developing them further.
LASER BEAM CUTTING
On separate paths
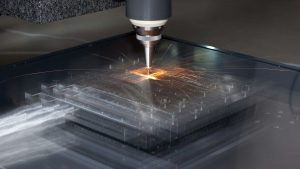
When it comes to cutting, laser technology demonstrates its unique flexibility: Through adapted process control, we can cut almost all materials in different thicknesses with the highest quality.
Due to the spatially limited energy input and its very high intensities, the laser beam is a universal tool for processing both metallic and non-metallic materials. Thus, with the help of laser technology, foils only a few micrometers thick can be cut just as well as centimeters thick sheets. By selecting a suitable laser wavelength, even highly reflective materials – copper, for example – can be processed well.
The development of high-speed fine cutting of thin sheets makes it possible to cut out even the finest contours with acute angles and the thinnest webs by means of adapted laser system technology and process control.
The blz staff has extensive expertise in the following areas:
– Laser cutting and structuring of metallic inserts to create thermoset hybrid structures.
– High-speed fine cutting
– Cutting of 3D components
– Cutting of glasses, ceramics and semiconductor materials
PRECISION MACHINING
Not superficial at all
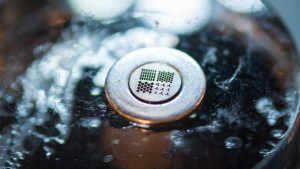
The market for ultrashort pulse applications is growing. Especially in the electronics and mobile communications industries, there are a wide variety of applications for laser technology. Ultra-short pulsed laser systems with outstanding beam properties enable high-precision and fast micro material processing. Coupled with high ablation efficiency, we can also optimally process thermally highly sensitive materials and generate free-form geometries using suitable processes. Extensive know-how in laser processes on ultra-short time scales, simulation, optics development, laser beam guidance and shaping, and prototype system design allows us to offer a wide range of services in precision machining:
– Generation of ordered micro- and nanostructures on surfaces and in volume
– Cold machining of any materials
– Micro-drilling of holes up to 20 μm in diameter
Equipped with modern short-pulse and ultrashort-pulse lasers, we process a wide variety of materials. The structuring and modification of surfaces as well as cutting are typical tasks and focal points of our activities.
ADDITIVE MANUFACTURING
Individuality in series
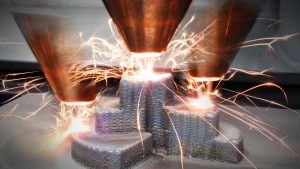
Time- and thus cost-saving product developments are important factors of economic success today. We use additive manufacturing technology to build three-dimensional functional and application prototypes, as well as finished tools and components, layer by layer.
Additive manufacturing technology enables the production of individual components from powders, liquids or material layers of a variety of different materials. We are in the process of developing processes to be able to produce complete assemblies with additional electrical and optical functionalities.
By qualifying new materials, we want to expand the range of use of these generative processes and identify new applications. The following aspects are the focus of our work:
– Additive manufacturing of polymer components
– Laser beam melting of metals from the powder bed
– Laser powder cladding
– Realization of three-dimensional functional and application prototypes
– Generation of assemblies with electrical and optical functionalities
– Powder analysis, data preparation and post-processing
PROZESSANALYSE
Der gläserne Prozess
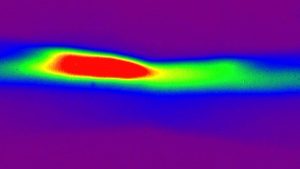
Indem wir individuelle Fertigungssituationen nachstellen und untersuchen, unterstützen wir Unternehmen bei der gezielten Lösung auftretender Probleme beim Einsatz von Lasertechnik. Das für die Analyse und Regelung der Prozesse zum Einsatz kommende systemtechnische Spektrum reicht von optischen, akustischen und mechanischen Sensoren bis hin zur Überwachung unter Einsatz von Hochgeschwindigkeits- und Thermokameras.
Mit Hilfe von Simulationen können zudem verschiedenste Szenarien abgebildet sowie Einflussfaktoren und deren Wirkung identifiziert werden. Um alle Möglichkeiten der Simulation auszuschöpfen, arbeiten wir daran, nicht nur einzelne physikalische Phänomene isoliert zu betrachten, sondern den kompletten Laserprozess in einem gesamtheitlichen Modell abzubilden.
Unser Leistungsportfolio im Überblick:
• Prozessüberwachung und Sensorik
• Modellbildung und Simulation
• Analytik
• Fehlerursachenerkennung
PROCESS ANALYSIS
The transparent process
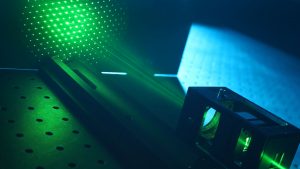
Many applications in laser metrology and laser material processing require an intensity distribution of the laser beam adapted to the application, such as a line-shaped or a top-hat intensity profile. In addition, flexible beam shaping and thus dynamic adaptation of the laser beam to the process opens up new possibilities for time- and cost-efficient processing of workpieces.
At the blz, various refractive and diffractive systems for shaping laser beams are being developed that are suitable for a wide range of applications in a large wavelength range from 193 nm to 10.6 µm and for both low and high power densities. In addition to laser beam homogenizers, the blz also offers multi-spot generators to increase throughput by means of parallel processing, such as perforating or structuring.
For flexible beam shaping, for example, light modulators (Spatial Light Modulator – SLM), micromirror arrays but also combined systems of different refractive and diffractive micro-optics are used.
The performance of the optics is tested and qualified in our laser material processing facilities. In this way, customer-specific applications can also be tested and optimized with the help of laser system technology.
Here is an overview of our offerings in the area of beam delivery and shaping:
– Customized development
– Prototype and small series production
– Reflective systems for micromachining
– Passive beam shaping (homogenizers, multi-spot generators)
– Active light modulators
OPTICAL SIMULATION
Light skilfully set in scene
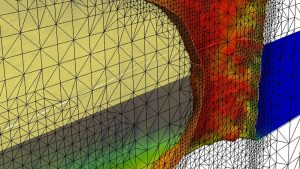
Optical simulation enables the influence of various parameters and manufacturing tolerances of optics and optomechanics to be precisely investigated and optimized even before the optical system is manufactured and implemented. For classical imaging and beam shaping optics with dimensions of several millimeters, long-established ray tracing programs are used. If the structures become smaller, wave-optical effects such as diffraction and interference must also be taken into account in the design. These effects can then be exploited specifically, for example to realize diffractive beam shaping elements.
The integration of real light sources and component surfaces is an important aspect of optical simulation. For the measurement of light sources, various measuring devices such as wavefront sensors or beam analysis cameras are available at the blz. Furthermore, it is possible to implement and investigate real components as well as tactile or optically measured topographies with the help of CAD interfaces. With our expertise in the field of optical simulation, we will find the right solution for your problem:
– Radiation and wave optical simulation
– Simulation of nanostructures
– Preparation and import of CAD data
– Measurement and implementation of real beam properties
– Optimization and tolerance analysis